筆者所在的中國空空導(dǎo)彈研究院一車間承制的某設(shè)備上所用的一種凸輪,自20世紀90年代以來一直采用靠模法加工。由最初經(jīng)過多次試制和手工修銼并裝機試驗,得到一個相對理想的模型,以后加工就采用按圖樣留一定余量先粗加工,然后有操作工人按模型進行靠模加工和修銼,最后把凸輪表面打磨光滑。這樣存在的問題就是加工難度高,對操作工人技術(shù)水平要求高,并且加工周期長,精度低,廢品率高。隨著數(shù)控機床和線切割設(shè)備的普及,采用線切割或數(shù)控加工的必要性和優(yōu)勢就越來越大。
一、凸輪原始圖樣要求和加工方法改進分析
1. 凸輪的原始圖樣資料和技術(shù)要求
凸輪的原始圖樣資料如圖1示,圖樣要求是:355°~185°為R55的圓弧,185°~235°為過渡段,235°~305°為半徑為R37的圓弧,305°~355°為過渡段。其中過渡段為5°均分,各特征點間通過樣條曲線連接。 VR%*8=
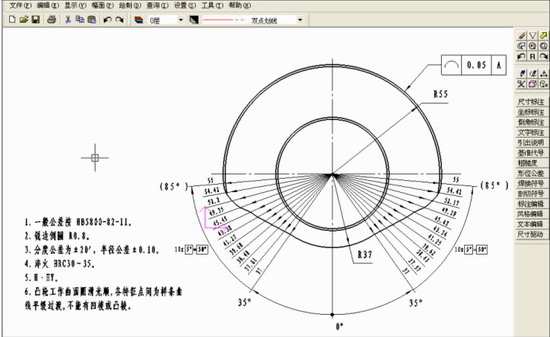
圖1 凸輪原始圖樣
2. 線切割加工試制和問題分析
我們的線切割機床所用的軟件為CAXA的電子圖板,按圖樣要求做出圖形,其中過渡段為先做出特征點,然后通過各特征點做樣條與兩段圓弧相連,這樣鉬絲的軌跡曲線就形成了。隨后上毛胚試制,加工后發(fā)現(xiàn)凸輪輪廓表面有棱,不順滑。分析其原因為:首先原始凸輪過渡曲線特征點數(shù)值不合適,因原圖樣描繪時間較早,為手工繪制的樣條曲線,造成曲線上特征點取值誤差大;其次就是圓弧與樣條曲線為直接相連,無法保證相切,故接縫處凸棱和凹棱較明顯。另外,線切割加工的不足是無法滿足表面粗糙度和加工效率的協(xié)調(diào)。
3. 數(shù)控銑床加工凸輪的分析
若采用配備了數(shù)控分度頭的數(shù)控銑床代替原來的靠模加工方法和線切割,不僅大大提高加工效率,降低了對操作工人的技術(shù)水平要求,并且可以提高加工精度和保證表面光滑度要求。
但因為凸輪的數(shù)控加工程序一般采用手工編制,其缺點是數(shù)控銑床軟件編譯采用直線插補,特征點間為直線連接,因手工編程方式的局限性,無法得到足夠的坐標點,這樣就導(dǎo)致加工后的凸輪輪廓有一定偏差,導(dǎo)致凸輪表面出現(xiàn)接棱。原圖樣是按5°為間隔進行分度,間隔較大,數(shù)據(jù)不能直接使用,若編程員對凸輪輪廓進行手工插值細化,則編程復(fù)雜,工作量太大,且數(shù)據(jù)校對困難,易出錯。若能通過軟件獲得數(shù)控銑床可識別的文件,則將大大簡化編程過程。
)>^